As a UX designer for Airbus, I was tasked with researching, and developing entire product discovery flow for an application that aims to minimize configuration mismatches and expired data improving the in-service configuration management.
Role
Product designer, Implementation Lead.
Duration
Jan 2024 - Present.
Project Scope
Design novel product concepts for in-service configuration management to minimize mismatches & expired data.
Deliverable
Conduct primary research, ideate and construct optimised product discovery flow prototype and feature recommendations.
BACKGROUND STORY
Airbus aircraft crashed due to misconfiguration.
"Possible human errors in documentation and verification".
On Jan 2015 Airbus A400 crashed due to software misconfiguration during installation of engine. The issue was only detected after takeoff, not during ground checks.
The incident highlighted the need for a more effective way to confirm airworthiness, raising several critical questions:
1. How can the installed parts in the aircraft be inspected more efficiently?
2. How is installation information currently managed?
3. Do paper-based documents make inspections more challenging?
4. How can configurations be verified more frequently and quickly?
5. How fast can a misconfiguration be detected?
6. Will digitalizing installation data help prevent misconfigurations?
7. How can installation data be cross-checked with expected configurations in real-time?
8. How can misconfigurations be identified immediately upon installation?
9. How can configuration errors be detected before an aircraft takes off?
our ask
“How can we make a go to solution for airlines to ensure fleet efficiency according to their configuration standards?”
Commonly seen configuration options:
Cabin Configuration: Three-class layout; larger planes: 3-4-3, smaller: 3-3.
Wing Configuration: Cantilevered (self-supporting) and braced (externally supported).
Tail Configuration: Conventional (most common), cruciform (for aft engines), and T-tail.
PROBLEMS
Airbus delivers a fleet of aircraft to airlines with the known configurations.
All the configuration and part details of every aircrafts in a fleet will be known to Airbus at the time of delivery to airlines.
The aircraft, originally matching Airbus' specifications, has been changed or modified in ways Airbus didn't record or expect. These changes can affect maintenance, performance, and compatibility.
There are numerous configuration mismatches and modification changes that aren't up to date in the records especially when Airbus have updates (mod changes) in their aircraft models. This outdated data complicates tracking the aircraft's status.
Paper-Based or Disconnected Systems – Potential inefficiencies in tracking configuration changes.
Design Process
Primary research
User interviews for user personas, qualitative and quantitative Analysis.
Secondary research
Market study, and competitor analysis.
Synthesis
User journey mapping, Design decisions, Hi-fi prototyping.
Target users

Gwen
Age: 38, Married with 2 children
Gwen is motivated by her passion for ensuring the safety of aircraft and the people who travel in them.
Gwen is a diligent quality assurance manager in the aircraft maintenance industry. She meticulously inspects aircraft parts to ensure they are in their correct positions, playing a crucial role in maintaining the safety and efficiency of airplanes.
🎯️️
Goal
Gwen’s ultimate goal is to streamline the aircraft inspection process.
☹️
Problems
Gwen struggles with the manual and time consuming process of inspecting aircraft parts, which often leads to human errors and delays in maintenance schedules
☹️
Pains
Frustration from repetitive and mundane tasks,
Risk of overlooking critical details due to manual inspection.
Pressure to meet tight maintenance deadlines.
🛑
Barriers
Concerns about the initial investment in new inspection technology.
Resistance to change from traditional manual methods.
Lack of awareness about available tech solutions in the market.
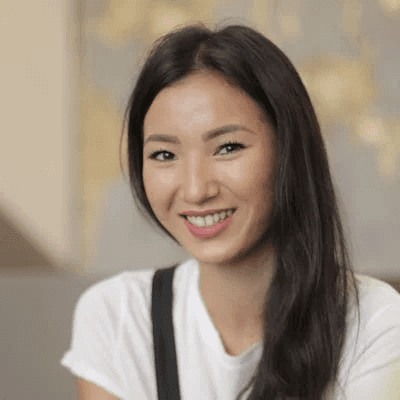
Melony
Age: 33, Married
Passion for aviation, dedication to safety, and commitment to excellence in fleet management.
Melony is a dedicated fleet manager responsible for ensuring the safety and airworthiness of aircraft under jer supervision. She meticulously inspects each aircraft to guarantee compliance with maintenance standards.
🎯️️
Goal
Ensuring aircraft safety, compliance with maintenance standards and improving fleet efficiency.
☹️
Problems
Melony struggles with the inefficiency and time consuming nature of manual aircraft maintenance checks, which often lead to delays and increased operational costs.
☹️
Pains
High risk of overlooking critical maintenance issues due to, manual processes.
Difficulty keeping up with evolving maintenance standards and regulations.
🛑
Barriers
Concerns about the technical complexity and implementation of new maintenance management systems.
Budget constraints for investing in advanced maintenance technology.
Resistance from team members to adopt new digital tools and processes.

Ally
Age: 35, Married with 1 child
Passion for aviation, commitment to safety, desire for professional growth.
Ally serves as a conscientious fleet manager at an airline, overseeing the safety and dependability of the aircraft under her care. She diligently examines each aircraft to ensure they meet stringent maintenance criteria.
🎯️️
Goal
Ally’s ultimate goal is to streamline the aircraft maintenance process, reduce the risk of safety incidents, and ensure the optimal performance of the entire fleet.
☹️
Problems
Ally struggles with the overwhelming amount of manual work required to track and analyse aircraft maintenance data, leading to potential oversights and inefficiencies int the maintenance process.
☹️
Pains
Risk of safety compliance issues.
Time- consuming manual inspections.
Difficulty om tracking maintenance history across multiple aircraft.
🛑
Barriers
Concerns about the effectiveness ad reliability of new maintenance technologies.
Budget constraints for implementing new maintenance software.
Resistance to change from existing manual processes.
Survery
70%
rely on manual checks and paper-based records for ensuring aircraft airworthiness.
65%
find the paperwork involved in maintaining aircraft airworthiness to be burdensome.
55%
face challenges in organizing and accessing aircraft maintenance data.
40%
struggle to meet all regulatory requirements for aircraft airworthiness.
60%
report occasional human errors that can impact aircraft airworthiness.
90%
value proactive maintenance and believe a digital solution could enable more proactive strategies.
User journey map
Developing a solution
How can we get all the part data of aircrafts?
Airbus has two source of data MIS and ACR to collect details of aircraft.
How can we determine which parts to fit where?
Airbus uses a unique identifier Functional Item Number (FIN) to identify the location of components on aircraft.
Each part has its own Part Number.
Airbus keeps track of all Allowed Part Numbers for FINs
USER flow to check the match
Major Design decisions
1
Airlines operate a range of Airbus aircraft families in their fleet, each with unique configurations.
Airlines identify an airplane using a hierarchy of Family>Type>Registration number.
Ability to filter and identify individual aircraft of each type by their respective Manufacturing serial number (MSN) + Aircraft registration number.
Ability to filter by airworthiness status if parts are wrong, to be analysed, or match according to the respective configurations.
Representation of A320 Family and its types.
A320 Family
Representation of registration number in an A318 airbus aircraft.
2
Designed a dashboard that provides a complete overview of the fleet's aircraft and their airworthiness status by comparing the details of parts and as allowed parts.
Sometimes airlines use a different part on an allowed FIN based on some condition which is a mismatch by intention, such part are to be analysed manually.
Thus overview of aircraft should either be:
Match (M): All parts attached correctly.
Wrong (W): At least one part is incorrect.
To be Analysed (A): At least one part pending analysis.
Design shows the ability to see the total number and percentage of parts that are matched, wrong, or to be analysed.


3
Created a display that offers an in-depth look at all parts of a chosen aircraft.
I found it essential to display the FIN along with the part details, such as the part description and number, since users typically identify individual parts this way (identified by observing excel sheets they use).
4
Designed a report view for a chosen aircraft which shows a report view to streamline the analysis of selected aircraft.
The goal was to guide users to a summary and then to a detailed view of their specific selection, whether they want to review all the wrong part or just the specific wrong part from any of the source MIS or ACR.
5
Designed an alert configuration system that lets a user keep track of the changes that are to be made on a specific part or aircraft.
Keeping track of all the changes and verifying them can be quite a challenge for a mechanic or lead technician. By enabling them to set up personalized alerts for parts that require their attention, users can stay informed with real-time updates through notifications and emails whenever any modifications are made to those parts.
turn outs
adopted the solution and are live users. Conversations are underway with additional operators to enrol the product.
The product is currently available at zero cost and includes paid premium features.
the outcome
80%
users report a significant reduction in time spent on manual checks, leading to faster operational processes.
95%
find that the streamlined paperwork has decreased administrative costs associated with maintenance documentation.
97%
indicate enhanced data organization and accessibility, resulting in quicker decision-making.
98%
feel more confident in meeting compliance, reducing the risk of fines and operational delays.
96%
experience fewer human errors which contributes to better safety records and customer trust, ultimately supporting revenue growth.
76%
find the application is helping to ensuring aircraft availability, directly impacting potential earnings.
Thanks for reading.
✉ msmanusankar98@gmail.com